Harnessing the Power of Induction Furnaces: A Revolution in Metal Melting and Processing

In the realm of industrial metallurgy, where the forces of heat and transformation forge the building blocks of modern infrastructure, lies the marvel of induction furnaces. Since their inception in the late 19th century, induction furnaces have been a driving force behind the seamless melting and processing of metals, shaping the very core of various industries. This blog post embarks on a journey into the heart of induction furnaces, exploring their inner workings, applications, and the transformative impact they’ve had on metal manufacturing processes.
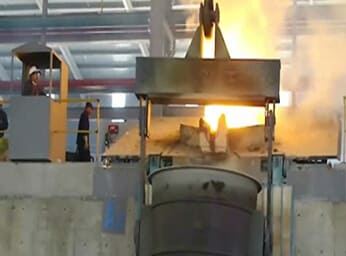
From the fiery crucibles of tradition to the electromagnetically charged chambers of innovation, the evolution of induction furnaces has been a fascinating testament to human ingenuity. Today, these high-tech marvels stand at the forefront of sustainable, energy-efficient metal melting, delivering unprecedented precision and versatility.
Join us as we unveil the inner workings of induction furnaces and delve into the critical roles they play across diverse sectors, from casting foundries to metal recycling facilities. From environmental benefits to enhanced productivity, the advantages of induction furnaces underscore their significance in shaping the future of the metals industry.
So, let us set forth on this exploration of induction furnaces, where science and engineering converge to unleash the true potential of metallurgical prowess. Embrace the heat, the magnetism, and the artistry that power the induction furnace revolution, leaving an indelible mark on the very foundation of our modern world.
The operation of an induction furnace involves a well-defined process to efficiently melt and heat metals. Here’s a detailed step-by-step explanation of how an induction furnace works:
1. Charging the Furnace:
The process begins with charging the furnace with the metal to be melted. The metal, often in the form of solid scrap, is placed in a crucible made of a refractory material. The crucible serves as a container for the metal during the melting process, ensuring it remains separate from the inductor coils and the induction coil’s magnetic field.
2. Closing and Sealing
After loading the metal into the crucible, the furnace is sealed to create a controlled environment. The closure helps maintain the required temperature and prevents heat loss during the melting process.
3. Power Supply
The next step involves connecting the induction coil to a power supply. The power supply provides an alternating current (AC) that flows through the inductor coil, creating a rapidly changing magnetic field. The inductor coil is typically made of copper, as it has excellent electrical conductivity and low resistance, which ensures efficient energy transfer to the metal.
4. Electromagnetic Induction
When the AC current passes through the inductor coil, it generates a powerful electromagnetic field. This changing magnetic field induces electrical currents, known as eddy currents, within the metal inside the crucible. The magnitude of these currents depends on the magnetic permeability and resistivity of the metal being melted.
5. Heat Generation
As the eddy currents circulate within the metal, they encounter resistance, causing the metal to heat up rapidly. The electrical energy from the induced currents is converted into heat, elevating the metal’s temperature. Since the heat is generated directly within the metal, the process is highly efficient, with minimal energy loss.
6. Melting
As the metal reaches its melting point, it transitions from a solid to a liquid state. The temperature is carefully monitored and controlled to ensure the metal melts evenly and does not overheat or burn. Once the entire metal charge has melted, the furnace can be used for various applications, such as casting, foundry work, or heat treatment.
7. Alloying
If the production requires the creation of specific alloys, additional elements are added to the molten metal. These alloying elements can alter the properties of the metal, making it suitable for specific industrial applications.
8. Tapping
After the desired melting process is complete, the molten metal is ready for use. The furnace is tilted or otherwise manipulated to allow the liquid metal to flow out of the crucible and into a suitable receptacle or mold. This process is known as tapping.
9. Refractory Maintenance
Refractory materials lining the furnace and crucible are subjected to extreme heat and wear during each melting cycle. Therefore, periodic maintenance and replacement of these materials are essential to ensure the furnace’s longevity and proper functioning.
Conclusion:
Induction furnaces have become indispensable in modern metalworking industries due to their efficiency, precision, and environmental advantages. The detailed process outlined above highlights the engineering marvel behind induction furnaces, which have transformed the way we melt and process metals, paving the way for innovative and sustainable metal production methods.