Building with Air: The Fascinating Journey of AAC Block Manufacturing
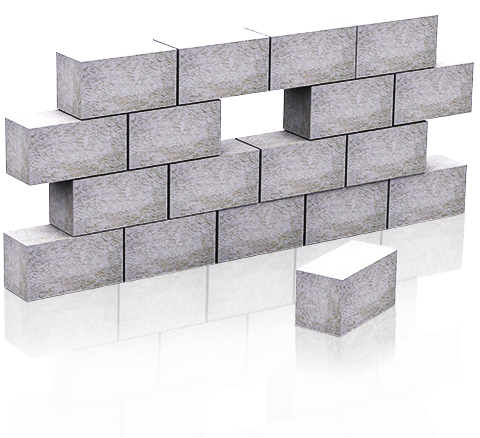
The manufacturing process of Autoclaved Aerated Concrete (AAC) blocks involves a combination of raw materials, precise chemistry, and a unique curing method. Here’s an elaborate overview of the AAC block manufacturing process:
1. Raw Materials Preparation:
The first step is to gather the essential raw materials, which typically include cement, lime, finely ground silica sand, water, and a small amount of aluminum powder. These ingredients are carefully selected to ensure consistency in the final product’s quality.
2. Mixing the Ingredients:
The raw materials are mixed in predetermined proportions in a concrete mixer. The addition of aluminum powder is a crucial step, as it acts as a foaming agent that generates hydrogen gas when it reacts with the alkaline elements in the cement and lime.
3. Foaming and Expansion:
The homogeneous mixture of ingredients is poured into molds of specific sizes and shapes. As the aluminum powder reacts with the cement and lime, hydrogen gas is produced, creating numerous tiny air bubbles within the mixture. This process is known as foaming and results in the expansion of the material.
4. Casting and Initial Curing:
The expanded mixture is poured into molds and left to rise for a short period. During this time, the hydrogen gas generated by the reaction causes the mixture to expand further, taking the shape of the mold. This initial curing phase allows the AAC to gain strength.
5. Autoclaving:
After the initial curing, the molds are transferred to an autoclave, a large pressure vessel. The autoclave is sealed, and steam is introduced under high pressure, creating a high-temperature and high-pressure environment within. The combination of pressure and steam triggers a second chemical reaction known as autoclaving.
6. Second Curing (Autoclaving):
During autoclaving, the calcium silicate hydrate (C-S-H) compound forms, which gives the AAC blocks their unique cellular structure and strength. This process also ensures that the material becomes stable, with minimal moisture content.
7. Cooling and De-molding:
Once the autoclaving process is complete, the molds are removed from the autoclave and allowed to cool down. The cooling process takes a few hours to prevent thermal shock. Once cooled, the AAC blocks are removed from the molds, and any excess material is trimmed off.
8. Quality Control:
Before the AAC blocks are ready for the market, they undergo thorough quality checks to ensure they meet the required standards. These tests include compressive strength, density, dimensional accuracy, and moisture content evaluations.
9. Packaging and Distribution:
After passing quality control, the AAC blocks are packaged and prepared for distribution. They are transported to construction sites, retailers, or building material suppliers for use in various construction projects.
The manufacturing process of AAC blocks combines chemistry, technology, and precision to produce a lightweight, eco-friendly, and durable building material that has gained popularity for its versatility and sustainability in the construction industry.