From Grains to Gains: Decoding the Journey of Feed Mills
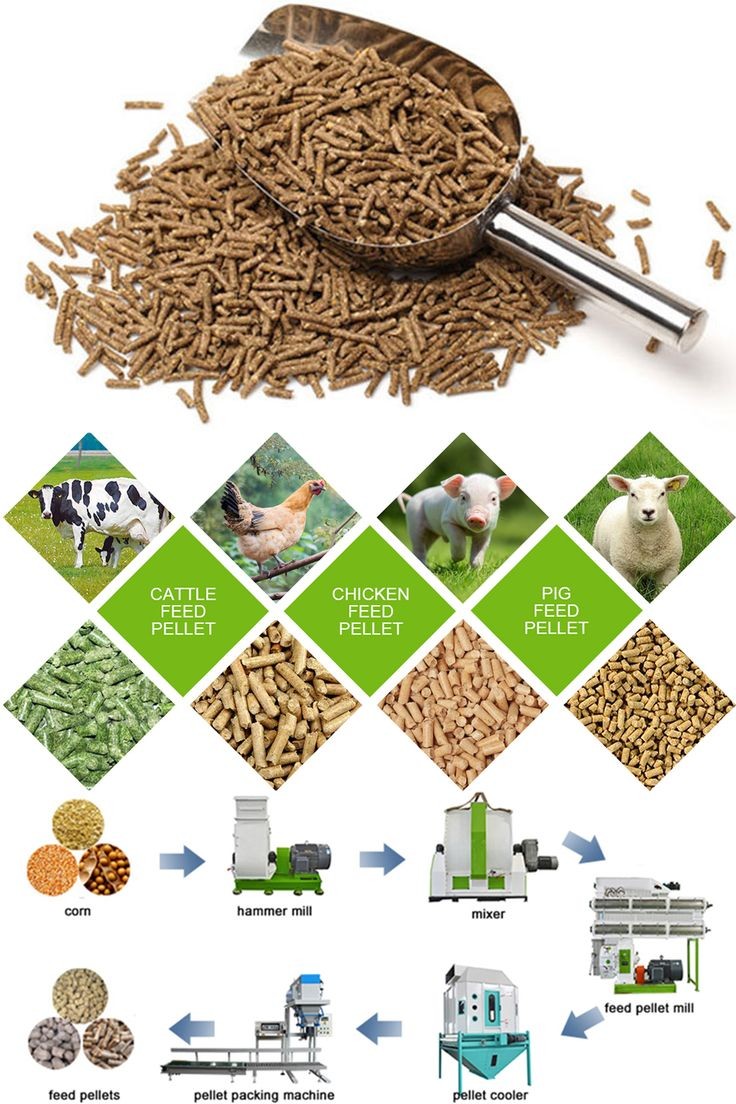
In the heart of modern agriculture, where the sustenance of livestock and the quality of our food supply converge, lies the intricate world of feed mills. These unassuming yet vital facilities stand as the architects of balanced nutrition, transforming raw ingredients into carefully formulated feeds that fuel the health, growth, and productivity of livestock around the globe. As we peer into the inner workings of feed mills, we uncover a journey that marries science, precision, and sustainability to create the sustenance that sustains us all. From the moment raw materials arrive at the doorstep to the final packaging of nutrition-packed pellets, the process unfolds with precision, ensuring that each animal is nourished with the right blend of nutrients for optimal well-being. Join us on a journey through the stages that shape the essence of feed mills – where science and agriculture harmonize to nourish both livestock and the lives they touch.
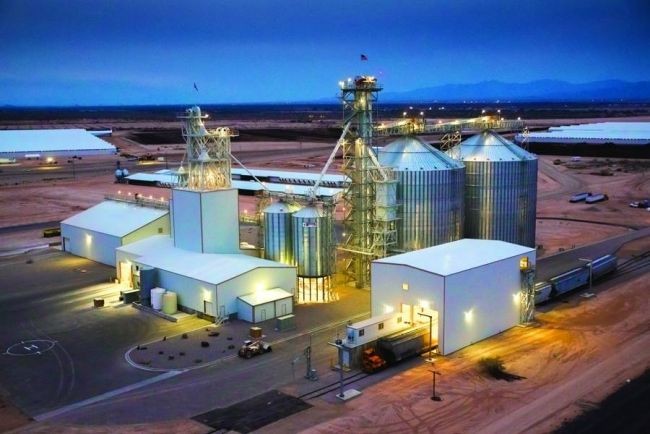
Certainly! The process involved in a feed mill is a multi-step procedure that transforms raw ingredients into nutritionally balanced animal feeds. Let’s take a detailed look at each step of this intricate process:
1. Raw Material Intake and Storage:
The first step involves receiving and storing raw materials. Ingredients like grains (corn, wheat, barley), protein sources (soybean meal, fish meal), fats, minerals, and vitamins are delivered to the feed mill. Quality checks are performed on these materials to ensure they meet the desired standards for nutrient content and purity. Once approved, the materials are stored in silos or bins until they are ready for processing.
2. Grinding:
Raw materials often have varying particle sizes, which can affect digestibility and feed consistency. Grinding involves reducing the size of these ingredients to a uniform particle size. This process not only enhances digestibility but also improves the mixing efficiency of the ingredients.
3. Mixing:
The ground ingredients are then thoroughly mixed to create a homogenous blend. Achieving a uniform mixture is crucial to ensure that each animal receives a consistent balance of nutrients in every bite of feed. Specialized mixing equipment ensures proper distribution of ingredients.
4. Batching and Scaling:
In this step, the mixed ingredients are weighed and measured according to the specific formulation for the type of animal feed being produced. Accurate scaling is essential to maintain the nutritional integrity of the final product.
5. Steam Conditioning:
Some feed formulations require steam conditioning. This process involves adding controlled amounts of steam to the mixture. Conditioning enhances the texture of the feed, increases its palatability, and improves the gelatinization of starches for better digestibility.
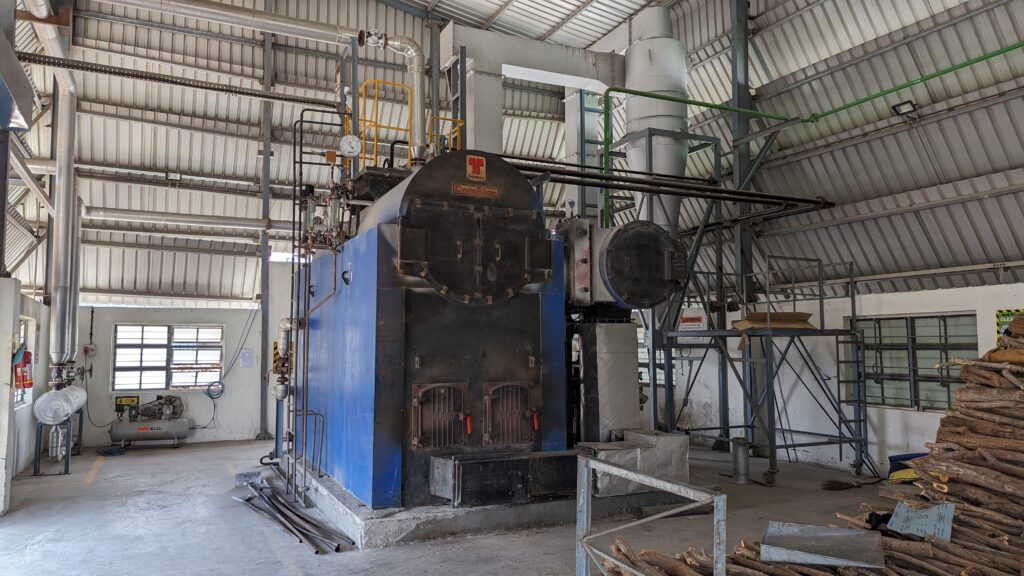
6. Pelleting or Extrusion:
Pelleting and extrusion are processes that transform the mixture into more manageable and uniform forms. Pelleting involves compressing the mixture into pellets using a pellet mill. Extrusion uses heat, pressure, and steam to create a more expanded and dense feed product. Both processes enhance feed quality, improve nutrient utilization, and reduce feed wastage.
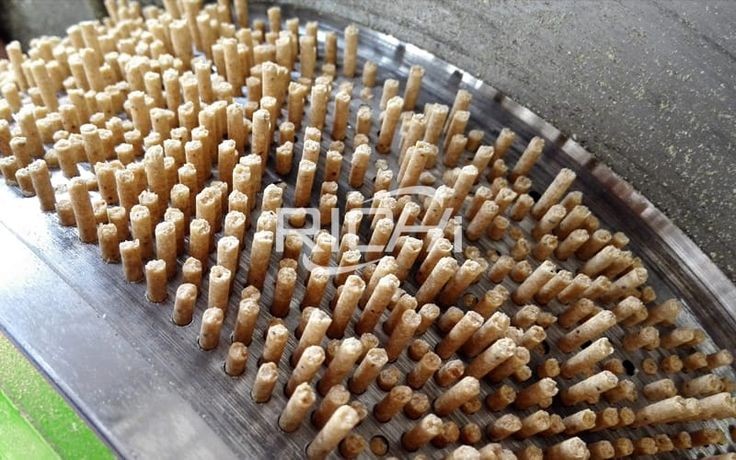
7. Cooling and Drying:
After pelleting or extrusion, the feed pellets can be hot and moist. Cooling is crucial to prevent spoilage and maintain pellet integrity. Coolers use controlled airflow to bring down the temperature of the pellets. Drying may also be necessary to reduce excess moisture.
8. Screening and Sifting:
The cooled and dried pellets are screened and sifted to remove any fines or broken pellets. This ensures that the final product is of consistent size and quality.
9. Coating and Additives:
Some feeds require additional coatings to enhance palatability, improve shelf life, or provide medication. These coatings may include fats, oils, flavors, and other additives.
10. Quality Control and Testing:
Quality control is maintained through regular testing of both raw materials and finished products. Laboratory analysis ensures that nutrient levels are accurate and consistent, meeting the intended formulation. Quality checks also extend to factors like pellet durability, particle size distribution, and absence of contaminants.
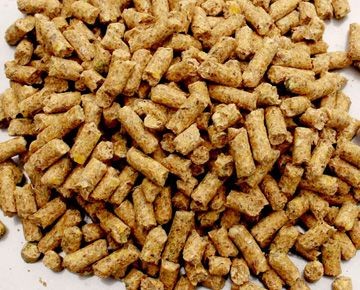
11. Packaging and Distribution:
The final step involves packaging the processed feed into bags, totes, or bulk containers suitable for distribution. Proper packaging preserves feed quality and prevents contamination during transportation and storage.
12. Environmental Considerations:
Modern feed mills often incorporate measures to minimize their environmental impact. These can include waste management systems, air emissions control, and sustainable practices like utilizing renewable energy sources.
In essence, the process involved in a feed mill is a meticulously planned and executed series of steps that ensure the production of high-quality, nutritionally balanced feeds for various livestock species. Each stage contributes to the overall health and productivity of animals, which in turn plays a vital role in supporting our food supply chain.