Unveiling Sustainable Solutions: Recovering Waste Heat in the Textile Industry
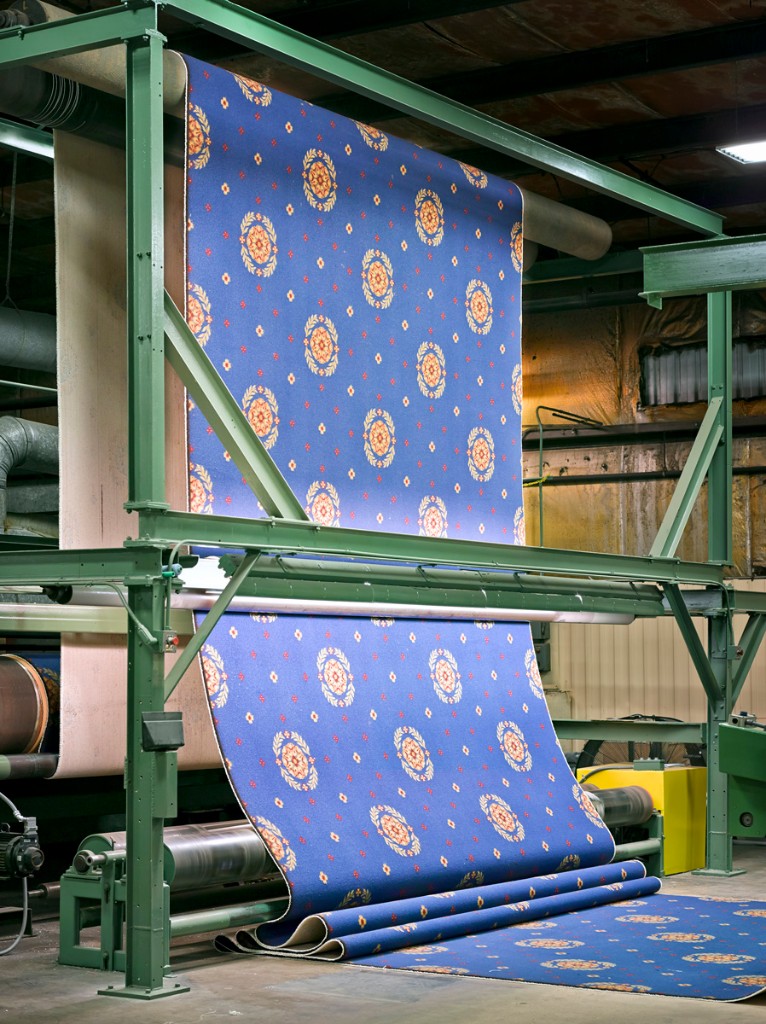
The textile industry plays a significant role in global manufacturing, providing a wide range of products that touch every aspect of our lives. However, this industry is also known for its substantial energy consumption and generation of waste heat. As the world strives for more sustainable practices, finding innovative ways to recover waste heat in the textile industry becomes imperative. In this blog post, we will explore some ingenious ideas that offer promising solutions for harnessing and reusing waste heat, thereby contributing to energy efficiency and environmental preservation.
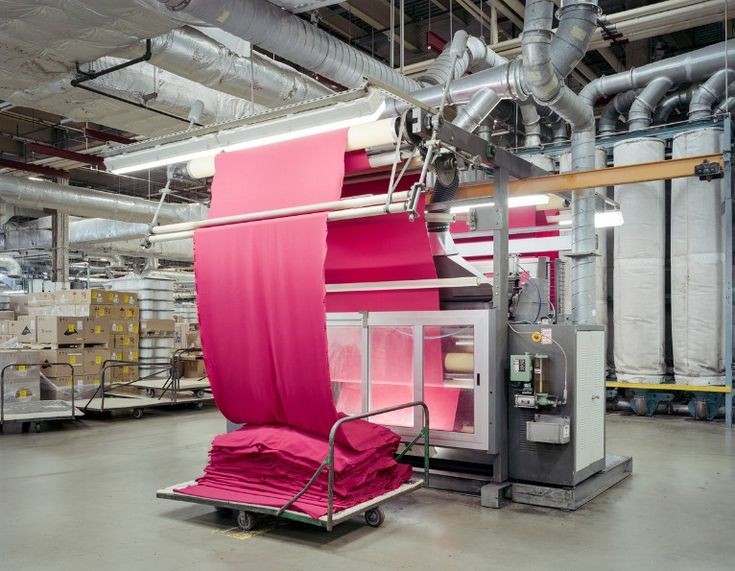
1. Heat Recovery from Dyeing and Finishing Processes:
Dyeing and finishing processes in the textile industry often involve heating water and chemicals to achieve the desired colors and textures. This results in the generation of significant amounts of waste heat. Implementing heat exchangers can help capture and transfer this heat from the hot effluent to the incoming cold water. The pre-heated water can then be used in subsequent processes, reducing the energy required for heating and leading to substantial energy savings.
2. Combined Heat and Power (CHP) Systems:
CHP systems, also known as cogeneration, are a powerful solution for waste heat recovery. In a textile manufacturing facility, CHP systems can utilize waste heat generated during power generation to provide both electricity and heat for the manufacturing processes. By simultaneously producing electricity and utilizing the generated heat, CHP systems can drastically enhance energy efficiency and reduce greenhouse gas emissions.
3. Heat Recovery from Exhaust Air:
Textile manufacturing involves a variety of machinery that produces exhaust air laden with waste heat. Installing heat recovery systems, such as air-to-air heat exchangers, can capture the heat from exhaust air and use it to preheat incoming fresh air. This not only reduces the energy demand for space heating but also improves indoor air quality by ensuring proper ventilation.
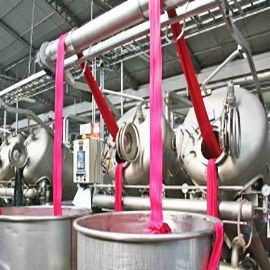
4. Waste Heat-to-Steam Conversion:
In textile production, steam is often used for various processes, including dyeing, drying, and finishing. Waste heat-to-steam conversion systems can utilize excess heat to generate steam, which can then be used for these energy-intensive processes. This approach not only conserves energy but also minimizes the consumption of water, another critical resource in the textile industry.
5. Integration of Solar Thermal Systems:
Solar thermal systems can be integrated into textile manufacturing facilities to supplement the heating requirements of various processes. By capturing solar energy through thermal collectors, these systems can provide an additional heat source, reducing the reliance on conventional heating methods and waste heat recovery systems.
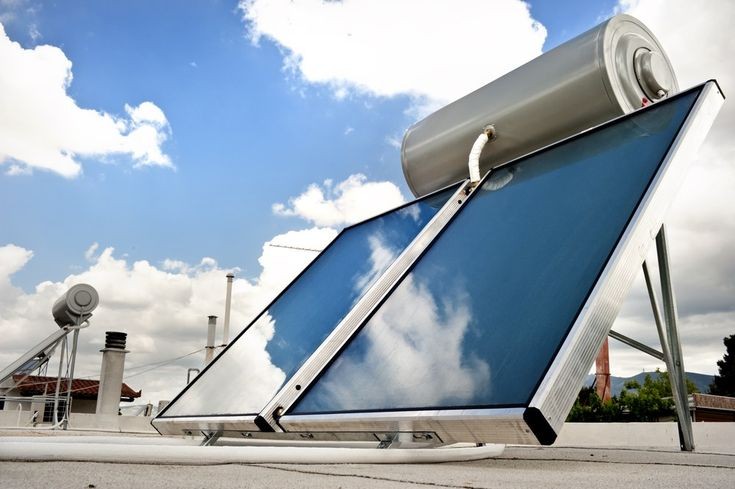
Conclusion:
The textile industry, like many others, faces the imperative of adopting sustainable practices to reduce its environmental impact and energy consumption. Recovering waste heat presents an exceptional opportunity to achieve these goals. By implementing innovative technologies such as heat exchangers, CHP systems, and solar thermal integration, textile manufacturers can effectively capture and reuse waste heat, leading to enhanced energy efficiency, reduced operational costs, and a greener footprint. As the industry continues to evolve, embracing these ideas for waste heat recovery will undoubtedly pave the way towards a more sustainable and environmentally conscious future.